Tech Helps Keep Retail Distribution Moving
Critical Needs in the COVID Era
- By [ Jess Dankert ]
- 07/28/2020
In many cases, ecommerce spikes or changes in replenishment needs have required hiring and rapid onboarding in distribution centers and other retail facilities. But how to train large groups efficiently in an era of social distancing and minimizing contact? Enter out-of-the box approaches like virtual training and distance learning.
As part of the industry’s COVID-19 response, Yale Materials Handling has made its Handle With Care® video training resource available to all, free of charge. Though created by Yale, these resources are brand agnostic, and allow retailers—or warehouse managers in any industry—to get lift truck operators up to speed quickly and safely, to help fulfill strict OSHA requirements.
“Finding skilled labor is one of our top challenges,” commented a supply chain executive at a major grocery retailer, “and these training resources have helped us get our new hires up to speed faster, and also practice social distancing at the same time.”
Indeed, social distancing has changed protocols through retail organizations. Not only do DC (and store) associates need to be mindful of limiting contact with co-workers; if an associate tests positive, it’s necessary for managers to engage in a painstaking process of contact tracing to alert others who may have been exposed. Solutions like Macondo Vision can help backstop and automate this work.
Originally created to multiply productivity in a warehouse environment, Macondo’s computer vision solution has found a second mission—monitoring associates’ social distancing, screening body temperatures, and tracking contact patterns.
Piloted in several companies’ warehouses in the past few months, the solution is now being scaled—as retailers and others plan for the “long haul” of operating safely in an extended COVID era. One general manager of a large DC observed: “Providing visibility into things we couldn’t see before has shed light on things we didn’t even know were problems allowing us to increase productivity and provide a safer work environment.”
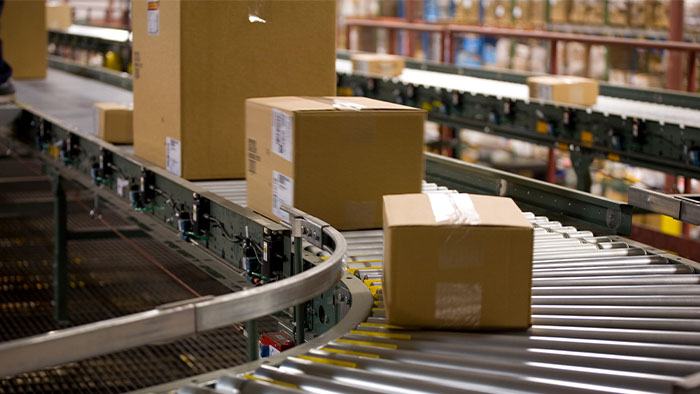
Speaking of automating, current events have added a new dimension to the pre-pandemic debates about robotics and automation in DCs. Labor shortages and availability, coupled with the challenges of social distancing, have made some retailers consider bringing in robots to help carry the load—especially where peak-like shifts to e-commerce have dramatically affected the demands on DCs.
Flexible solutions with relatively rapid deployment times have an edge in these uncertain times. 6 River Systems’ collaborative mobile robots (or “cobots”) named Chuck promise greater labor efficiency in order picking, increased employee engagement, and the ability to design zones and workflows to keep associates naturally socially-distanced in the DC. Using analytics, the software automatically determines the timing and routes of associates’ picking patterns, optimizing the number of associates and limiting in-aisle interactions.
“We were easily able to adjust the Chucks’ programming to manage the number of people and interactions on
the floor, helping achieve our safety and distancing goals,” noted the operations manager of a 50,000-sq ft e-commerce fulfillment center. “We also saw an immediate shift in employee morale and improved productivity after implementing robotic automation: a 38% increase in pick velocity and a marked decrease in employee turnover.”
In the face of unprecedented disruption, retail supply chain executives have had to quickly pivot operations— and sometimes rebuild their strategic plans. Technology has helped keep retailers keep their associates safe, and employed, while making sure customers can get the things they need in the COVID era.
Tags
-
Technology & Innovation
-
Supply Chain